FIRE ENAMEL
Fire enamel, sgraffito ceramics, painted enamel, stencil enameling, embedded an relief enamel making at affordable prices in Florida and in California.
You can find my fire enamel work and arts in this page, including my new and older fire enamel painting and fire enamel creations.
Fire enamel is a craft and fine art technique which consists of fusing a powdered colored glass material onto a substrate, known as a recipient, usually metal, which is then organically fused to the recipient and colorfully decorates its surface.
Fire Enamel is a decorative material used in the jewelry industry for thousands of years. In the course of its development, a number of techniques have evolved. By the 20th century, prominent figures in other artistic fields had discovered the potential of enamel.
If you have any questions about my artwork made with the fire enamel technique or would like to place an order, please email sooscsilla.glass@gmail.com or call me at
+36 30 557 6233
FIRE ENAMEL WORKS – GALLERY
FIRE ENAMEL WORKS – VIDEOS
Stained Glass Work | Video Link |
Fire Enamel: Crossroad Stations |
To view all my Fire Enamel related work please visit the main gallery page and under SELECT CATEGORY select the subcategory “FIRE ENAMEL » » »”
FIRE ENAMEL TECHNIQUE

Fire Enamel Artist In Florida – Csilla Soós
There are many different techniques of enameling, common to all of them is that dry or wet, slurried enamel powder is deposited in some way on a substrate surface in a thin layer and then the whole is fired in a kiln. If wet material is used, it is dried beforehand.
The back of the base is usually covered with a layer of counter enamel and fired first to avoid deformation. The base plate is often covered with a base enamel, on which the actual work is placed. The firing temperature is 700-820 °C.
Enameling can be divided into two main types, painting enameling, and jeweler’s enameling, according to the way the enamel is applied. Painting enamels include, for example, stencil enameling, sgraffito, and the painting enamel technique.
The sub-groups of jeweler’s enameling are cloisonne, inlay enameling, and relief enameling. The types of cloisonne enamel include ribbed enamel, twisted enamel, filigree enamel, Transylvanian enamel, and azure enamel. Subtypes of embedded enamel include flat relief and mixed enamel.
- In the case of stencil enameling, a stencil is placed on the fired base enamel with a cut-out of the desired shape, through which the enamel powder is sifted onto the plate and is then fed into the furnace.
- The word sgraffito means to scratch or scrape. The enamel is applied in layers to the enamel picture made using this technique; the outlines are scratched into the top enamel, which has not yet been fired, the circumscribed surface is scratched back and then fired again. This process can be repeated several times, the scraping always revealing the previous layer, the already fired enamel.
- When creating painted enamel, no engraving or frames are used, but the enamel slurry is applied to the flattened plate with a brush, as painters apply paint. In this case, the artist needs to know what color the enamels will be after firing.
- When making cloisonne, compartments are filled with enamel. The compartments are delimited by metal strips soldered to the base plate. These can be of several types. If they have a rectangular cross-section, they are called ribbed enamel, if they are made of twisted wire, they are called twisted enamel. In the case of filigree enamel, the inner fields of thin flattened wires or filigree wires are enameled, the outside of the pattern being enamel-free. In Transylvanian enamel, the compartments are not closely spaced. In the case of azure or openwork enamel, the base plate is removed, the enamel-filled compartments transmit light like window panes, the result is similar to stained glass.
- In the case of embedded enamel, the grooves and recesses of the design engraved in the base are filled with enamel. Flat relief enamel is made by carving the base in relief and then covering the whole work with enamel. The color of the enamel then appears lighter or darker according to the reliefs. In the case of mixed enamel, the larger indented fields are divided into smaller fields by metal strips.
- In the case of relief enamel, the main feature is the partial or total enameling of high reliefs or completely plastic reliefs.
– source – Wikipedia
THE MILLENNIA-OLD HISTORY OF ENAMEL
Fire enamel has been a technique in the art of jewelry-making for thousands of years. The first glass melts are thought to have been an accidental by-product. Later, these colored ‘stones’, formed by polishing, were deliberately used for decoration. We have real enameled ‘cloisonne’ jewelry artifacts from Egypt, I. century A.D. For centuries, the art of enameling was handed down from father to son, which was also a hindrance to progress.
In addition to the various types of enamel (openwork, ribbed, filigree, wire, twisted, recessed) that flourished in the Middle Ages, new possibilities were created as enameling techniques developed and were refined.
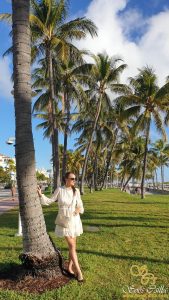
Fire Enamel Artist In Miami, Florida – Csilla Soós
This is how the technique of enamel painting developed in the 15th century, and later, in the Baroque period, miniature painting on enamel. Benvenuto Cellini, one of the most famous artists of the Renaissance, also made enameled decorative objects and wrote a book on the subject, entitled Lectures on Goldsmithing and Sculpture, which also describes the technique of enameling in detail.
The 19th century saw a real change in the context of overall industrialization, with the emergence of technical enameling, industrial enameling, as an industry in its own right, and the start of mass production. Contrary to previous conceptions, the artist was relegated to the background.
Only the Art Nouveau period brought a major revival in enameling, with jewelry and ornaments being the main products of the artisans. Nowadays, there is a revival of the ‘enamel art’, with a new approach to industrial enameling alongside the traditional old techniques, and more and more craftsmen are using industrial enamel raw materials in their creations.
If you have any questions about fire enamel making, or if you would like to place an order, please send an email to sooscsilla.glass@gmail.com or contact me at the following telephone number